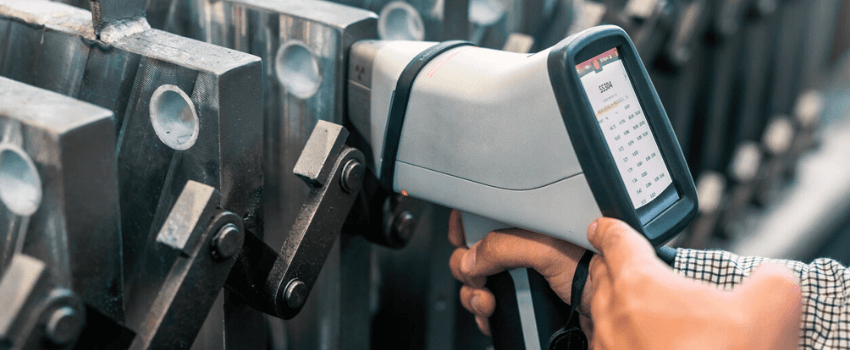
Positive Material Identification (PMI) is a critical, non-destructive, testing method used in many key industries to verify the chemical composition of materials, particularly alloys. This article explores the importance of PMI in ensuring material integrity and safety, plus leading analytical methods, industry standards, and the role of reference materials in PMI.
What is Positive Material Identification?
PMI is a non- or minimally destructive testing method used to verify the elemental composition of metal alloys. It plays a crucial role in ensuring that metallic components contain the correct percentage of key elements that directly impact material properties – such as corrosion resistance, and mechanical strength. PMI is commonly employed in major industries such as aerospace, petrochemical, power generation, and manufacturing, where material integrity is critical, and where the correct selection and application of materials are paramount for ensuring safety, reliability, and performance. Incorrect or inaccurate metal composition, whether intentional or accidental, can lead to catastrophic failures, serious financial losses, and even loss of life. But the correct use of PMI can help our leading industries to prevent such negative events.
Benefits of PMI
PMI is also vital for:
Quality Control : ensuring that materials meet specifications before and during manufacturing
Regulatory compliance : meeting standards and regulations set by relevant technical organisations
Failure prevention : reducing the risk of unexpected mechanical or chemical failures by identifying alloy composition correctly
Protecting the bottom line : adding upfront costs, but preventing much larger down-the-line expenses - including downtime, repairs, and potential litigation
Risk mitigation : minimising the likelihood of using counterfeit or substandard materials
Traceability : throughout the materials supply chain
PMI techniques
A number of analytical techniques are employed in PMI, each with their own advantages and limitations:
X-ray Fluorescence (XRF): High-energy X-rays excite atoms in the sample, causing them to emit fluorescent X-rays that are characteristic of their elemental composition. XRF is the most widely used PMI technique due to its portability, speed, and non-destructive nature.
Optical Emission Spectroscopy (OES): a high-energy spark excites atoms in the sample, causing them to produce emissions characteristic of each element present.
Laser-Induced Breakdown Spectroscopy (LIBS): A short laser pulse on the sample generates plasma, the emitted light from which is analysed to determine elemental composition. LIBS offers fast analysis and can be used for remote sensing.
Analytical Technique | Strengths | Limitations |
• Fast | • Less effective for light elements (e.g., C, B, Li, Be) | |
• High accuracy | • Creates a small burn mark | |
Laser-Induced Breakdown Spectroscopy (LIBS) | • Fast | • Lower accuracy compared to XRF and OES for some elements |
Industry standards for Positive Material Identification
When performing PMI, adherence to established industry standards is essential to ensure accuracy, reliability, and compliance with regulatory requirements. Expert bodies such as ASTM International (ASTM) and the International Organisation for Standardisation (ISO) have developed specific standards that outline best practices for PMI testing methods, equipment calibration, and data interpretation. Below are some standard methods relevant to PMI:
ASTM Standards
ASTM E1476: Standard Guide for Metals Identification, Grade Verification, and Sorting (which describes qualitative and quantitative methods to verify metal grades and identification, assisting investigators in selecting the best method for their application)
ASTM E415: Standard Test Method for Analysis of Carbon and Low-Alloy Steel by Spark Atomic Emission Spectrometry
ASTM E572: Standard Test Method for Analysis of Stainless and Alloy Steels by Wavelength Dispersive X-Ray Fluorescence Spectrometry
ASTM E1086: Standard Test Method for Analysis of Austenitic Stainless Steel by Spark Atomic Emission Spectrometry
ASTM E1999: Standard Test Method for Analysis of Cast Iron by Spark Atomic Emission Spectrometry
ASTM E2465: Standard Test Method for Analysis of Ni-Base Alloys by Wavelength Dispersive X-Ray Fluorescence Spectrometry
Industry-specific standards and guidelines
American Petroleum Institute API RP 578: Material Verification Program for New and Existing Alloy Piping Systems (a comprehensive guide for implementing PMI programmes in refineries and petrochemical facilities)
American Society of Mechanical Engineers ASME B31.3: Process Piping (containing requirements for material verification in petroleum, chemical, pharmaceutical and other critical piping systems)
Electric Power Research Institute (EPRI): Guidelines and Specifications for High-Reliability Fossil Power Plants - Best Practice Guideline for Manufacturing and Construction of Grade 92 Creep Strength Enhanced Ferritic Steel Components
The role of reference materials in PMI
Reference materials play a vital role in ensuring the accuracy and reliability of PMI testing. They are essential for calibrating analytical instruments such as X-ray fluorescence- and optical emission spectrometers. By providing known concentrations of target elements, reference materials establish the correlation between instrument signal and elemental concentration, ensuring that unknown samples are measured accurately.
Before an analytical method is used routinely, it needs to be validated for accuracy, precision, linearity, and detection limits. Reference materials are used to assess these parameters, helping to confirm that the method performs reliably for the intended application.
The different types of reference materials for PMI instruments include:
National Metrology Standards: issued by an authorised body like the US National Institute of Standards and Technology (NIST) or the European Union’s Joint Research Centre (JRC), they are considered to have the highest accuracy and traceability.
Certified Reference Materials (CRMs): defined by ASTM as a “Reference material characterised by a metrologically valid procedure for one or more specified properties, accompanied by a reference material certificate that provides the value of the specified property, its associated uncertainty, and a statement of metrological traceability.”
Reference Materials (RMs): again, in ASTM’s words, this is a material that is “sufficiently homogeneous and stable with respect to one or more specified properties, which has been established to be fit for its intended use in a measurement process.”
Setting-up Samples (SUS): also called check samples, recalibration samples or monitor samples, these are materials with known compositions used to verify instrument performance during routine testing.
Key questions to consider when choosing a PMI reference material
Q: What type of reference material is required by the method, or is appropriate for the application?
A: You should choose a reference material that is fit for purpose (i.e. suitable for its intended use).
Q: Does the composition of the reference material closely resemble the material to be tested?
A: A reference material that mimics the test material's characteristics in terms of matrix and analyte concentration range helps to confirm that the analytical method is performing correctly and providing accurate results.
Q: Is the CRM or RM supplier accredited to ISO 17034?
A: If you need a CRM or RM, make sure that the supplier is ISO 17034 accredited. ISO 17034 outlines the essential requirements for producers of reference materials to ensure consistency, reliability, and accuracy.
Explore LGC Standards metal alloy reference materials today
LGC Standards' metal alloy reference standards range provides 3,000+ high-quality, specifically designed, reference materials for accurate and reliable metal alloy analysis, using techniques such as XRF and OES.
|